Cleanroom: Comprehensive Guide to Design, Standards, and Applications
A comprehensive cleanroom guide covering design principles, global standards, and diverse applications across healthcare, pharma, and tech industries.
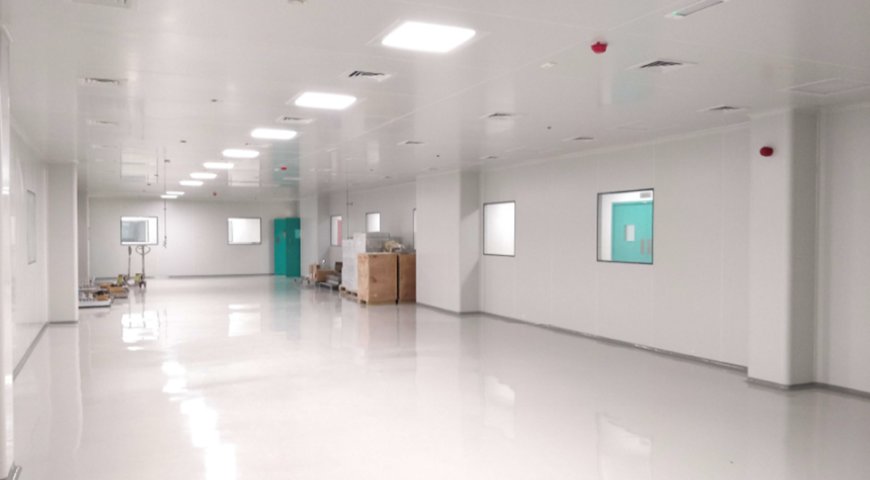
What is a Cleanroom?
A cleanroom is a controlled environment designed to maintain extremely low levels of particulates, airborne organisms, or chemical vapours. These rooms are essential in industries where even microscopic contamination can compromise products or processes, such as pharmaceuticals, biotechnology, aerospace, semiconductor manufacturing, and medical devices.
Key Cleanroom Standards and Classifications
Cleanrooms are classified based on the number and size of particles permitted per volume of air. The two main standards used globally are:
ISO 14644-1 Classification
- ISO Class 1-9: Defines cleanliness levels by the maximum allowable number of particles per cubic metre.
- ISO Class 5: Common for pharmaceutical aseptic processing.
- ISO Class 7-8: Standard for medical device assembly and electronics manufacturing.
Federal Standard 209E
Although superseded by ISO 14644, it remains referenced in some regions:
- Class 100 (equivalent to ISO 5)
- Class 10,000 (equivalent to ISO 7)
- Class 100,000 (equivalent to ISO 8)
Types of Cleanrooms
Hardwall Cleanrooms
These feature solid panels, aluminium or stainless-steel frames, and integrated utilities, offering durability for permanent installations in pharmaceutical and semiconductor facilities.
Softwall Cleanrooms
Constructed with clear vinyl curtains, these are cost-effective, modular, and suitable for ISO Class 7-8 applications such as assembly areas or packaging rooms.
Modular Cleanrooms
Prefabricated panels enable quick installation, scalability, and reconfiguration, ideal for expanding manufacturing needs or rented facilities.
Ballroom Cleanrooms
Large open areas with minimal internal walls, designed for flexible production layouts and multiple processes under a single cleanroom classification.
Cleanroom Design Considerations
Air Filtration and HVAC
- HEPA Filters: Remove 99.97% of particles ≥0.3 microns.
- ULPA Filters: Remove 99.9995% of particles ≥0.12 microns, used in ISO Class 1-3 cleanrooms.
- Airflow Patterns: Laminar flow for stringent environments; turbulent flow for less critical applications.
- Air Changes per Hour (ACH): Ranges from 20 (ISO 8) to over 400 (ISO 3).
Cleanroom Materials
- Walls: Aluminium honeycomb panels, stainless steel, or coated steel.
- Flooring: Vinyl, epoxy, or raised access flooring with antistatic properties.
- Ceiling Grid: Suspended aluminium grids supporting filters, lights, and utilities.
- Lighting: LED or fluorescent fixtures, fully sealed to prevent particle accumulation.
Entry Systems
- Airlocks and Gowning Rooms: Prevent contamination during personnel entry.
- Pass-Through Chambers: Transfer materials without disrupting cleanroom pressure or cleanliness.
Environmental Controls
- Temperature and Humidity: Maintained within ±2°C and 40-60% RH for product stability.
- Pressure Differentials: Positive pressure to protect from contamination; negative pressure for hazardous containment applications.
Cleanroom Validation and Certification
Validation ensures cleanrooms meet design standards before operational approval.
Key Tests Include:
- Airborne Particle Count Testing
- HEPA Filter Integrity Testing (DOP/PAO test)
- Airflow Volume and Velocity Measurements
- Recovery Tests (contamination removal efficacy)
- Containment Leak Tests
Validation should follow ISO 14644-3 protocols and be conducted during:
- As Built: Cleanroom complete, no equipment installed.
- At Rest: Equipment installed, but no personnel.
- Operational: Fully functional with personnel present.
Cleanroom Maintenance Protocols
Daily Tasks
- Cleaning floors and surfaces with lint-free mops and wipes.
- Checking pressure gauges and filter differentials.
Weekly Tasks
- Cleaning walls and ceilings.
- Inspecting gowning rooms and airlocks for contamination risks.
Monthly Tasks
- HEPA/ULPA filter inspections.
- Airflow pattern checks.
Strict adherence to SOPs (Standard Operating Procedures) ensures compliance and product safety.
Cleanroom Applications Across Industries
Pharmaceuticals
- Sterile formulations, injectable manufacturing, and aseptic filling require ISO Class 5 or better.
Biotechnology
- Cell culture labs and genetic testing facilities depend on contamination-free environments.
Semiconductor and Electronics
- Wafer fabrication and microchip assembly occur in ISO Class 1-5 cleanrooms to prevent yield losses due to microscopic particles.
Medical Devices
- Assembly and packaging of implants, surgical kits, and diagnostic devices under ISO Class 7-8 cleanrooms to comply with FDA and ISO standards.
Aerospace and Defence
- Satellite assembly, optical component manufacturing, and precision instrumentation require ultra-clean environments.
Emerging Trends in Cleanroom Technology
Modular Prefabricated Cleanrooms
Companies are adopting modular cleanrooms for rapid deployment, cost savings, and scalability, especially in contract manufacturing and emerging biotech startups.
Energy-Efficient Designs
Integration of variable speed fans, advanced HVAC controls, and LED lighting to reduce operational costs without compromising cleanliness.
Automation and IoT Integration
Real-time monitoring of temperature, humidity, and particle counts improves operational efficiency, predictive maintenance, and compliance readiness.
Sustainable Materials
Use of recyclable aluminium, low-VOC coatings, and energy-saving filters to meet environmental targets and corporate sustainability goals.
Choosing a Cleanroom Supplier
When selecting a supplier, consider:
- Experience in regulated industries
- Turnkey design, engineering, and installation capabilities
- Validation and certification support
- After-sales service and maintenance programs
Conclusion
Cleanrooms are critical infrastructure for pharmaceuticals, semiconductors, medical devices, biotechnology, and aerospace industries, where contamination control defines product integrity and regulatory compliance. Investing in precise design, stringent maintenance, and future-ready modular solutions ensures operational excellence and competitiveness.