The Precision and Purpose of Embroidery Digitizing in Today’s Apparel Industry
Discover how embroidery digitizing enhances precision, efficiency, and creativity in the apparel industry. Learn about its role, process, and modern applications.
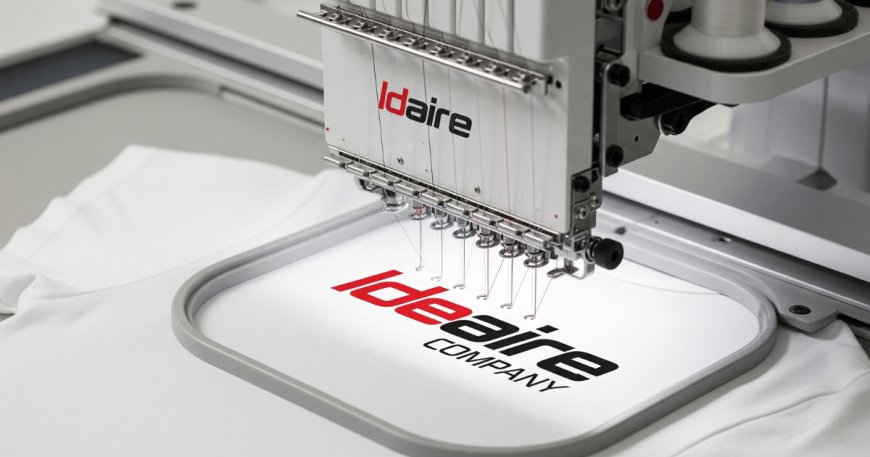
Introduction
The textile and fashion industries have long embraced embroidery as a mark of craftsmanship and identity. From traditional hand-stitched monograms to complex commercial logos, embroidery adds a touch of uniqueness to garments and accessories. But with demand for speed, consistency, and intricate designs, manual embroidery methods alone can’t meet the needs of modern manufacturing. This is where embroidery digitizing steps in as a transformative solution.
Embroidery digitizing is the technical process that translates a design or image into a format that embroidery machines can read. While it might sound simple on the surface, this process requires both artistic insight and technical precision. In this article, we explore how digitizing works, its advantages, and where it’s making the biggest impact.
What Is Embroidery Digitizing?
At its core, embroidery digitizing is the process of converting an artwork, whether it's a logo, monogram, or illustration, into a machine-readable embroidery file (such as DST, PES, or EXP formats). This involves using specialized software to map out every stitch, determine thread paths, and optimize tension, direction, and density.
Unlike scanning or printing, embroidery digitizing is not automatic. The digitizer must understand the design intent, the behavior of the fabric, and how stitches interact with different materials to produce clean, durable results.
For high-quality outcomes, businesses often turn to experienced providers like True Digitizing, known for precision work across varied industries.
How the Digitizing Process Works
The digitizing process typically includes the following key stages:
-
Artwork Preparation
The original design is cleaned up and adjusted to make it suitable for stitching. Fine details that won’t translate well into thread are simplified or modified.
-
Pathing and Stitch Assignment
The digitizer assigns stitch types (such as satin, fill, or run stitches), directions, and orders of operations, ensuring the embroidery machine follows a logical and efficient path.
-
Underlay Settings
Underlay stitches help stabilize the fabric and set a foundation for the top layers of stitching, preventing puckering or distortion.
-
Density and Compensation Adjustments
Stitch density is adjusted based on the fabric type. Compensations are added to ensure the design doesn’t shrink or stretch after stitching.
-
File Conversion and Testing
The design is saved in the appropriate format, and test runs are conducted to verify quality before full-scale production.
Benefits of Embroidery Digitizing
Digitizing brings multiple benefits to the table:
-
Precision and Consistency
Digitizing ensures every stitch is exactly where it needs to be, regardless of how many times the design is replicated.
-
Speed and Efficiency
Once a design is digitized, it can be stitched hundreds or thousands of times with the same level of quality and speed.
-
Complex Design Capabilities
Advanced digitizing allows for intricate details, shading effects, and textures that were nearly impossible with manual methods.
-
Customizability
Businesses can tweak logos, add personalization, and create variations without having to start from scratch each time.
Industries That Rely on Digitizing
The reach of embroidery digitizing extends across many sectors:
-
Corporate Branding
Embroidered uniforms and promotional merchandise often begin with a professionally digitized logo.
-
Fashion and Streetwear
Brands use digitizing to achieve distinctive design aesthetics for caps, jackets, hoodies, and more.
-
Team and Sportswear
Jerseys, hats, and gear feature digitized names, numbers, and logos that stand up to wear and washing.
-
Retail and Small Businesses
Independent apparel creators and Etsy sellers often rely on digitizing to produce small batches of custom embroidered products.
Choosing the Right Digitizing Service
Not all digitizing services are equal. Poorly digitized files can result in misaligned stitching, thread breaks, or fabric damage. High-quality digitizing requires:
-
Deep knowledge of embroidery mechanics
-
Experience with different fabrics and threads
-
Use of industry-standard software
-
A commitment to test and revise files
Working with a professional team like True Digitizing ensures you get optimized, production-ready files that meet your specific requirements.
The Future of Embroidery Digitizing
As embroidery machines evolve and software becomes more advanced, the potential for creative and commercial embroidery expands. Some trends shaping the future include:
-
3D and Puff Embroidery
Digitizing techniques for raised stitching effects are becoming more popular, especially in fashion and headwear.
-
Sustainable Practices
Efficient stitch pathing and waste reduction are gaining importance as brands seek to minimize environmental impact.
-
Cloud-Based Digitizing
Remote collaboration and cloud file sharing are making it easier to submit artwork and receive digitized files quickly.
Final Thoughts
Embroidery digitizing is a cornerstone of modern textile decoration. From boosting production efficiency to unlocking design potential, it plays a crucial role in bridging the gap between imagination and wearable reality. Whether you're a large apparel manufacturer or an independent creator, investing in skilled digitizing services is essential for achieving top-tier embroidery results. To learn more about embroidery digitizing, visit True Digitizing and explore how precision meets creativity in every stitch.